How To Troubleshoot F-105 Thunderchief Systems
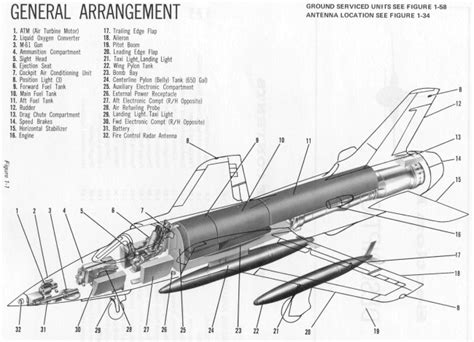
The F-105 Thunderchief, a iconic supersonic fighter-bomber of the Cold War era, was renowned for its robust design and exceptional combat capabilities. However, like any complex aircraft, it was not immune to system malfunctions and technical issues. Effective troubleshooting of these systems is crucial for ensuring the aircraft's airworthiness, optimizing its performance, and maintaining operational safety. In this comprehensive guide, we will delve into the methodologies and best practices for troubleshooting F-105 Thunderchief systems, covering its electrical, hydraulic, fuel, and avionics systems, as well as providing expert insights and real-world applications.
Introduction to F-105 Thunderchief Systems

The F-105 Thunderchief is equipped with a range of sophisticated systems, including electrical, hydraulic, fuel, and avionics systems, each playing a critical role in the aircraft’s operation. The electrical system, for instance, powers the aircraft’s avionics and communication equipment, while the hydraulic system controls the landing gear, flaps, and brakes. Understanding the intricacies of these systems is essential for effective troubleshooting. Thorough knowledge of system interdependencies is vital to identify and isolate faults efficiently. Furthermore, schematic diagrams and technical manuals are indispensable tools for any maintenance personnel tasked with troubleshooting the F-105 Thunderchief.
A key aspect of troubleshooting is the ability to analyze system performance data, which involves interpreting data from various sensors and system monitors to pinpoint anomalies. This skill, combined with hands-on experience with the aircraft’s systems, enables technicians to diagnose issues accurately and efficiently. It’s also important to consider the environmental factors that could affect system performance, such as extreme temperatures or humidity levels.
Electrical System Troubleshooting
Troubleshooting the electrical system of the F-105 Thunderchief involves a systematic approach, starting with the identification of symptoms and progressing through a series of checks and tests to isolate the fault. This may include visual inspections of wiring and connectors, continuity tests to verify circuit integrity, and functional tests of electrical components. The use of multimeters and other specialized test equipment is also crucial for measuring voltage, current, and resistance in electrical circuits.
It’s essential to follow a structured troubleshooting methodology to avoid missing critical steps or introducing new faults. This methodology should be based on the aircraft’s technical documentation and should include checks for common issues such as faulty relays, fuses, and grounding problems. By methodically ruling out potential causes, technicians can efficiently identify and rectify electrical system faults.
System Component | Troubleshooting Steps |
---|---|
Generator | Check voltage output, inspect for signs of wear or damage |
Transformer Rectifier Units (TRUs) | Test for proper voltage conversion, inspect cooling system |
DC-DC Converters | Verify output voltage, check for overheating or malfunctioning components |

Hydraulic System Troubleshooting
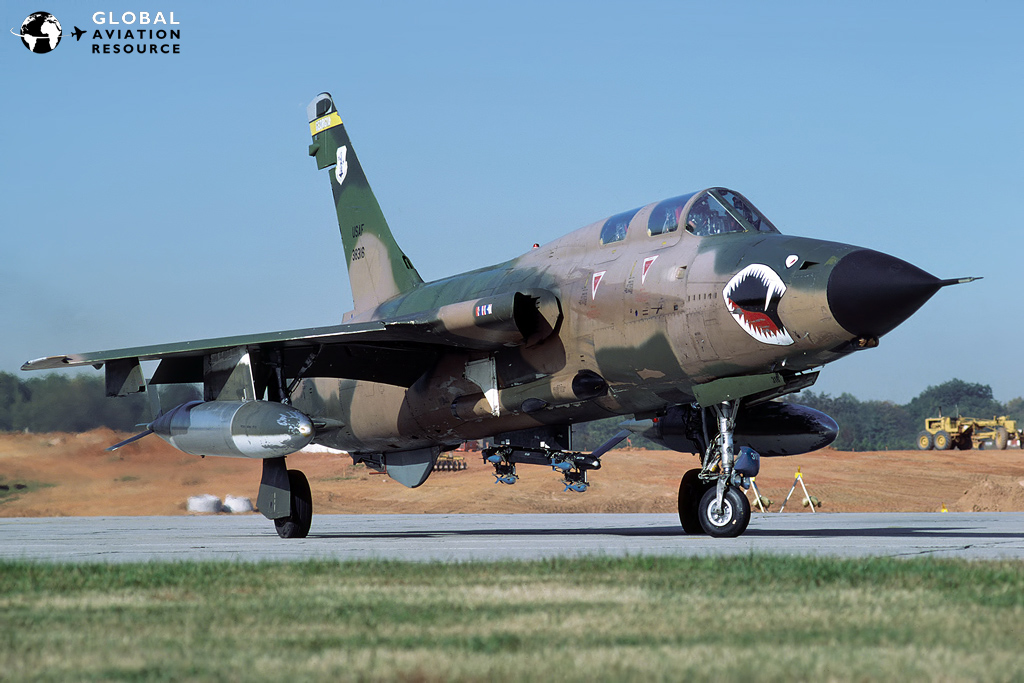
The hydraulic system of the F-105 Thunderchief is critical for controlling various flight surfaces and landing gear. Troubleshooting this system requires attention to detail and a systematic approach. Leak detection is a crucial step, as hydraulic fluid leaks can lead to system failure. Technicians should also perform pressure tests to verify system integrity and flow tests to check for restrictions in the hydraulic lines.
Understanding the principles of hydraulic fluid dynamics is essential for diagnosing issues related to fluid pressure, flow rate, and viscosity. Moreover, being familiar with the aircraft’s hydraulic system schematics helps in tracing faults to specific components or sections of the system. Regular maintenance and inspection of hydraulic components, such as pumps, valves, and actuators, can prevent many issues before they become critical.
Fuel System Troubleshooting
Troubleshooting the fuel system involves checking for issues related to fuel flow, pressure, and quality. Fuel filter inspections and tank integrity checks are essential for ensuring that fuel can flow freely and without contamination. Technicians should also be aware of the signs of fuel system icing and know how to apply corrective actions to prevent or mitigate such issues.
A critical aspect of fuel system troubleshooting is the ability to interpret fuel system performance data, which may involve analyzing fuel flow rates, pressures, and temperatures. This data can provide valuable insights into the health of the fuel system and help technicians identify potential problems before they lead to engine failure or other critical issues.
What are the common signs of a malfunctioning hydraulic system in the F-105 Thunderchief?
+Common signs include decreased system pressure, fluid leaks, and difficulties in extending or retracting the landing gear or flight surfaces. These symptoms can indicate problems with hydraulic pumps, valves, or lines and require immediate attention to prevent system failure.
How often should the electrical system of the F-105 Thunderchief be inspected and maintained?
+Regular inspections and maintenance of the electrical system are crucial for preventing faults and ensuring reliability. This should be done in accordance with the manufacturer's recommendations and may include daily checks, routine maintenance tasks, and periodic overhaul of components.
Performance Analysis and Future Implications
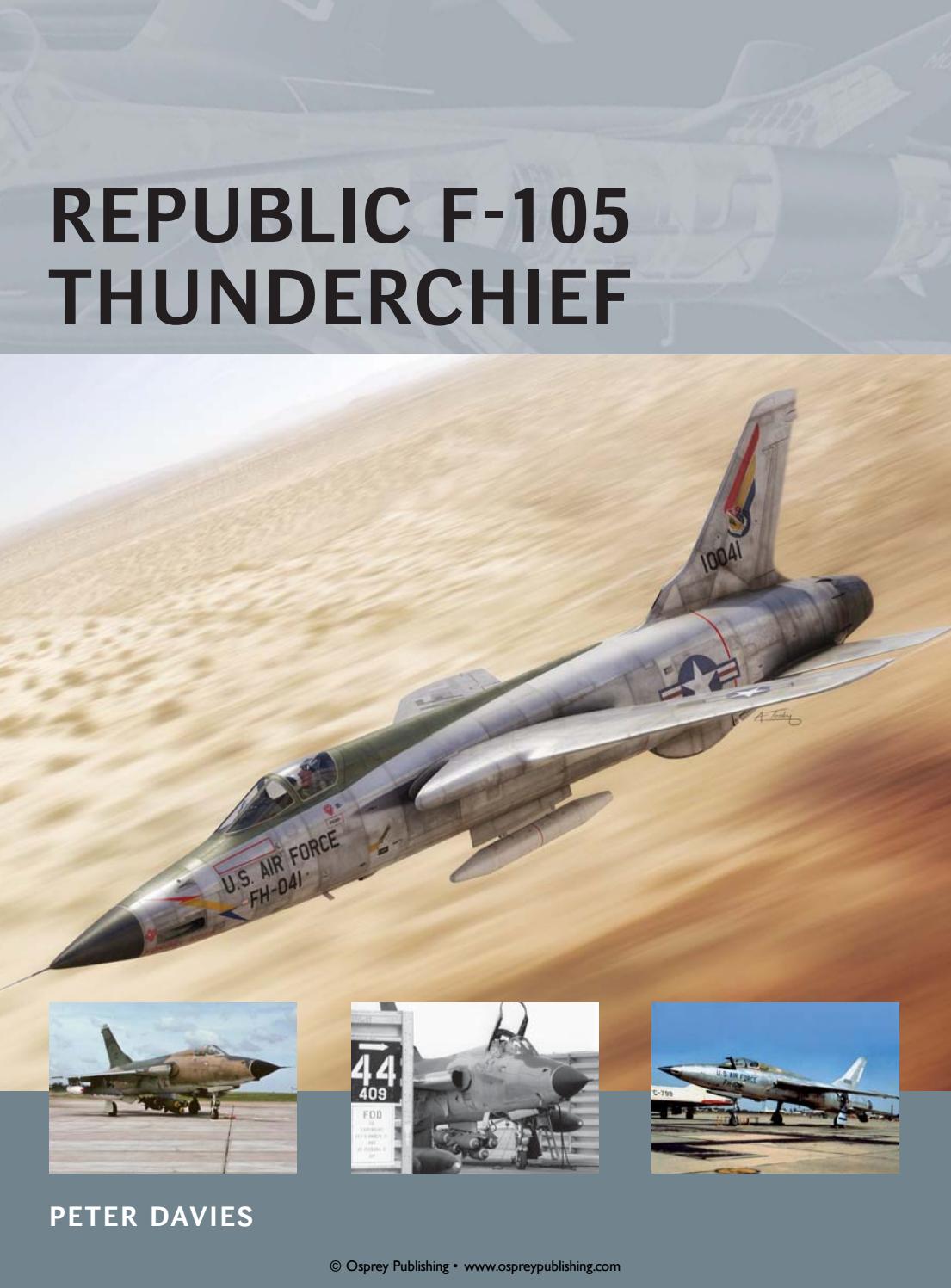
Effective troubleshooting of the F-105 Thunderchief’s systems not only ensures the aircraft’s immediate airworthiness but also contributes to its long-term performance and reliability. By analyzing system performance data and identifying trends, maintenance personnel can predict and prevent potential issues, reducing downtime and operational costs. Moreover, the lessons learned from troubleshooting these systems can inform the design and development of future aircraft, leading to more robust and reliable aviation technologies.
The integration of advanced materials and technologies into aircraft design is expected to further enhance system reliability and efficiency. However, this will also introduce new challenges for troubleshooting, as technicians will need to adapt to novel system architectures and failure modes. Therefore, continuous training and professional development are essential for maintaining the expertise required to troubleshoot complex aircraft systems effectively.
In conclusion, troubleshooting the systems of the F-105 Thunderchief requires a deep understanding of the aircraft’s technical specifications, a systematic approach to fault identification, and the ability to interpret complex system performance data. By combining these skills with real-world experience and adherence to best practices, technicians can ensure the optimal performance and safety of this iconic aircraft, setting a high standard for aviation maintenance and repair.