What Tools Do Warehouse Specialists Use?
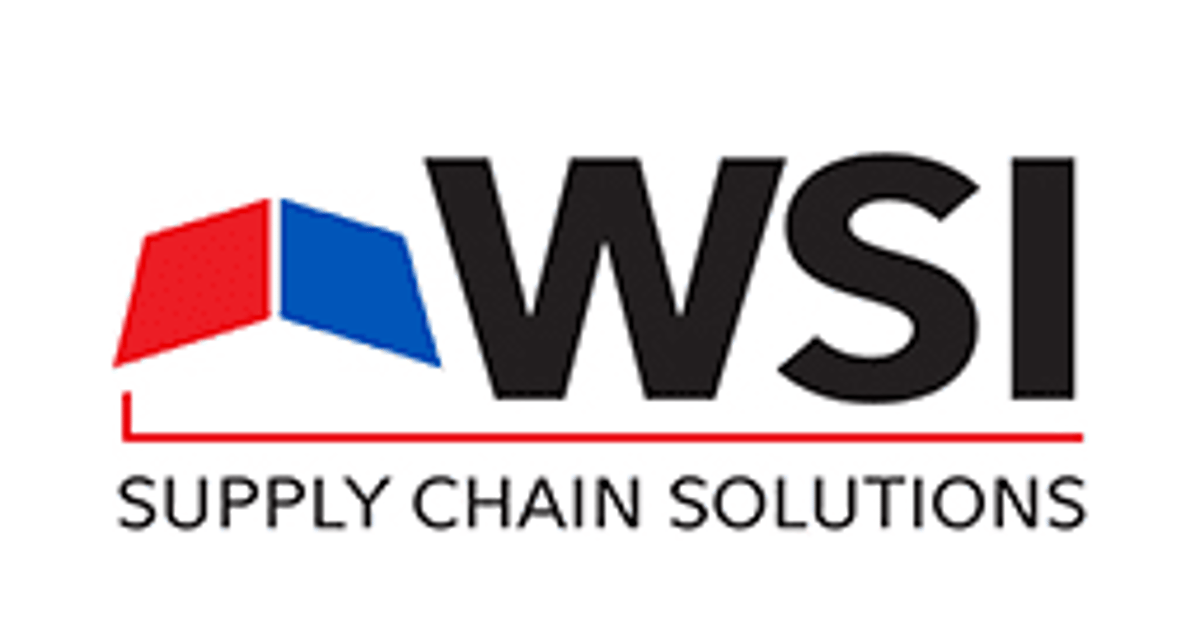
Warehouse specialists play a crucial role in the logistics and supply chain management of various industries, ensuring the efficient receipt, storage, and dispatch of goods. To perform their tasks effectively, they rely on a range of tools and technologies designed to streamline warehouse operations, enhance productivity, and improve accuracy. From manual handling equipment to sophisticated software solutions, the array of tools at their disposal is vast and varied. Understanding the specific tools and technologies used by warehouse specialists is essential for optimizing warehouse performance and meeting the demands of an increasingly complex and competitive market.
Introduction to Warehouse Tools and Technologies
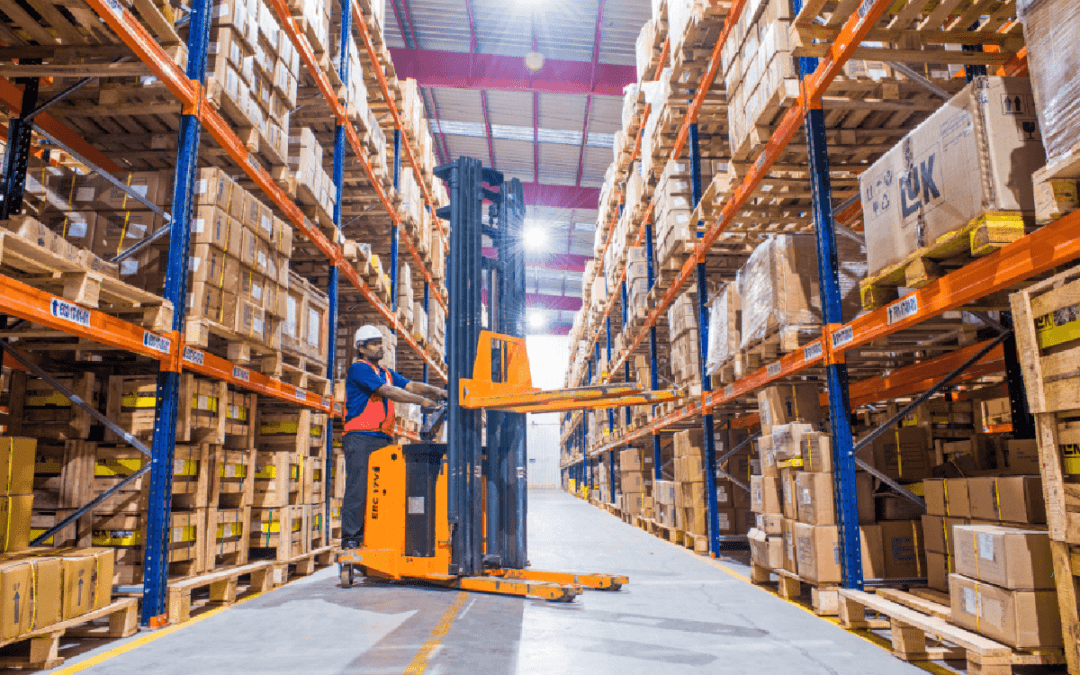
The role of a warehouse specialist encompasses a broad spectrum of responsibilities, including inventory management, order fulfillment, and maintaining the overall organization of the warehouse. Given the diversity of tasks involved, the tools used can be broadly categorized into manual handling equipment, automated systems, and software solutions. Manual handling equipment such as forklifts, pallet jacks, and conveyor belts are staples in most warehouses, facilitating the movement and storage of goods. Meanwhile, automated storage and retrieval systems (AS/RS) and warehouse management systems (WMS) represent the technological backbone of modern warehouses, enabling efficient inventory tracking, optimized storage, and streamlined operational processes.
Manual Handling Equipment
Manual handling equipment is fundamental to the daily operations of a warehouse, allowing specialists to handle goods with precision and care. This category includes:
- Forklifts: For lifting and moving heavy pallets and goods around the warehouse.
- Pallet jacks: Used for transporting pallets over short distances and within tight spaces.
- Conveyor belts: Facilitate the movement of goods along a fixed path, reducing manual labor.
- Hand trucks and dollies: Essential for the manual transportation of smaller, lighter items.
These tools are vital for the efficient handling of goods and are often the first point of contact in the warehouse workflow. Their effective use not only enhances productivity but also helps in reducing the risk of damage to goods and minimizing the occurrence of workplace injuries.
Automated Systems
Automated systems have revolutionized warehouse operations by introducing a level of precision and speed that manual handling alone cannot match. Key automated systems include:
Automated Storage and Retrieval Systems (AS/RS): These systems use machines to store and retrieve goods from defined storage locations, significantly increasing storage density and reducing retrieval times. Barcode scanners and RFID tags are also integral to automated systems, enabling the quick identification and tracking of inventory. Additionally, pick-to-light and put-to-light systems guide warehouse specialists to the correct storage locations, further optimizing the picking and stocking processes.
Automated System | Functionality |
---|---|
AS/RS | Automates storage and retrieval of goods |
Barcode Scanners | Quick identification and tracking of inventory |
RFID Tags | Wireless tracking of goods and inventory management |
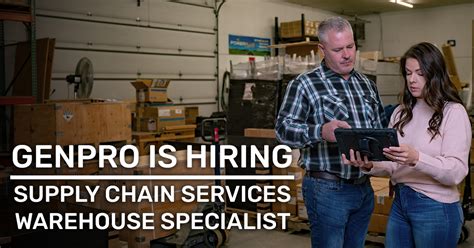
Software Solutions for Warehouse Management

Software solutions are the backbone of modern warehouse management, providing a centralized platform for managing all aspects of warehouse operations. Warehouse Management Systems (WMS) are designed to optimize inventory management, automate tasks, and provide real-time visibility into warehouse operations. These systems can integrate with existing enterprise resource planning (ERP) systems and transportation management systems (TMS), ensuring a seamless flow of information across the supply chain. Furthermore, inventory management software enables precise tracking of stock levels, automates reordering processes, and helps in minimizing stockouts and overstocking.
Technical Specifications and Performance Analysis
The performance of warehouse tools and technologies can be analyzed based on several key metrics, including inventory accuracy, order fulfillment rates, shipping times, and warehouse capacity utilization. For instance, a well-implemented WMS can significantly reduce inventory discrepancies and enhance order fulfillment rates, leading to improved customer satisfaction and reduced operational costs. Similarly, the use of automated systems can increase warehouse capacity by allowing for more efficient use of space and reduce labor costs associated with manual handling.
What are the primary benefits of implementing automated systems in a warehouse?
+The primary benefits include increased storage density, reduced retrieval times, enhanced accuracy, and lower labor costs. Automated systems can also lead to improved workplace safety by minimizing the risk of manual handling injuries.
How do Warehouse Management Systems (WMS) contribute to efficient warehouse operations?
+WMS contribute to efficient warehouse operations by providing real-time inventory tracking, automating tasks, optimizing storage and retrieval processes, and integrating with other supply chain systems. This leads to improved inventory accuracy, faster order fulfillment, and reduced operational costs.
In conclusion, the array of tools and technologies at the disposal of warehouse specialists is designed to address the complex challenges of modern warehouse management. By understanding and effectively utilizing these resources, warehouses can achieve higher levels of efficiency, accuracy, and customer satisfaction, ultimately contributing to the success of the entire supply chain.